ECONOMIE
Des bouteilles made in Sainte-Marie-la-Blanche
Par Nadège Hubert
Publié le 28 Juin 2024 à 07h33
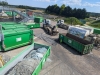
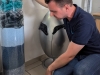
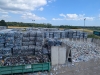
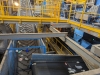
Avant de se retrouver sur nos tables, les bouteilles d’eau minérale ou encore de boissons sans alcool naissent chez des industriels. Pour fabriquer les préformes de bouteilles qui sortent de ses lignes de Sainte-Marie-La Blanche depuis 1998, Plastipak s’appuie sur son unité de retraitement des déchets de plastique.
Mais à quoi peuvent bien servir les grands silos qui trônent sur le site de Plastipak à Saint-Marie-la Blanche ? En arrivant sur le parking de l’usine, cette question s’est immiscée dans mon esprit. Avant que ma curiosité ne soit satisfaite, d’autres interrogations sont venues tenir compagnie à la première. Dans mon esprit, Plastipak était un simple producteur de bouteilles en plastique alors pourquoi toutes ces balles de déchets plastique triés et encerclés… « Depuis l’installation de l’entreprise en 1998, la première activité a été le recyclage et la transformation du PET, une catégorie de plastique » explique Jérémy Manigaud, responsable des opérations Plastipak, qui montre les différentes étapes de transformation du plastique.
Chaque année, l’industriel transforme 50 000 tonnes de bouteilles en plastique qui deviennent 40 000 tonnes de paillettes. Ces dernières sont lavées puis, par un procédé d’extrusion, deviennent granulés. « Nous achetons également des paillettes auprès de fournisseurs extérieurs pour obtenir ensuite environ 47 000 tonnes de granulés chaque année afin de réaliser, par injection, environ un milliard de préformes pour nos clients qui les changeront en bouteille dans leur processus de remplissage. » Le site Plastipak de Côte-d’Or s’est spécialisé dans les préformes de boissons telles que les eaux minérales, les jus de fruits ou encore les boissons gazeuses et non gazeuses sans alcool. « Nos clients font partis des majors du secteur. » Danone, Unilever, le groupe Coke ou encore Refresco réalisent ainsi 90 % du chiffre d’affaires de la filiale locale.
Dans les coulisses des bouteilles plastiques
Une fois les présentations faites et les explications données, il est temps de s’équiper pour trouver les réponses concrètes aux questions nées à l’arrivée. Casque, lunettes, chaussures de sécurité… Plastipak dispose d’un circuit pédagogique ouvert aux scolaires et aux étudiants. La visite commence donc par le centre éducatif autour du recyclage cofinancé par Coca Cola entreprise. « Nous accueillons environ 5 000 personnes par an pour ces visites. » Mon guide me conduit ensuite sur une passerelle en hauteur pour avoir une vue dégagée sur la multitude de balles de plastique recyclé qui attendent d’entrer dans le processus de tri de l’usine. « Nous retrions les balles pour être sûr de ne faire entrer que du PET que l’on pourra utiliser. En raison des erreurs de tri, nous avons en moyenne 29 % de rejet. » Voici la réponse à ma seconde question. Il en reste une en suspens.
D’étape en étape
L’une des difficultés majeures du processus concerne les étiquettes présentes sur les bouteilles plastiques. Sans réglementation spécifique, elles peuvent tout aussi bien être en papier collé sur la bouteille ou en plastique. « Une machine a pour mission de diluer la colle avec de l’eau et un additif auquel nous avons ajouté une opération mécanique pour gratter l’étiquette. » Quid des bouchons ? « Ils deviendront également paillettes mais, d’une autre sorte de plastique, ils seront isolés par un principe de flottaison pour devenir granulés chez un partenaire situé en Bourgogne. »
Sur les tapis roulants, les bouteilles mais aussi différents déchets plastiques défilent sous nos yeux pour passer d’une étape à une autre. Une phase de rinçage sera suivie par un tri des éléments métalliques éventuels. « Nous trions ensuite les paillettes par transparence. » Les paillettes seront par la suite fondues dans une extrudeuse avant d’être filtrées une dernière fois. « Le filament de paillettes fondues est ensuite refroidi avant d’être coupé pour devenir des granulés. Ils passeront ensuite dans une centrifugeuse pour retirer l’eau nécessaire à cette opération. » Les étapes se suivent mais ne se ressemblent pas. Vient ensuite la phase de cristallisation afin de former une enveloppe autour des granulés. « Pour éliminer toute contamination éventuelle, il y a également une étape de polycondensation sous azote. Cette opération dure 16 heures à 200 degrés pour enlever les impuretés de l’échelle du micron. » Il ne reste plus qu’à refroidir les granulés à température ambiante tandis que le laboratoire contrôle aussi bien leur couleur que leur qualité. « Ils rejoignent alors un silo de stockage pour alimenter nos lignes d’injection en interne mais aussi être vendus en vrac à des clients qui ont également intégré le processus d’injection. » Et voilà à quoi servent les silos extérieurs. Le mystère s’éclaircit.
Toujours pas de bouteille
Les opérations de recyclage occupent la majeure partie du site mais il reste toutefois l’activité d’injection qui fabrique les préformes qui seront expédiées aux clients par camion pour rejoindre les lignes de remplissage et prendre la forme finale de bouteille. L’industriel dispose de moules adaptés aux formes souhaitées par ses différents clients. « Nous pouvons réaliser des préformes avec du PET 100 % recyclé ou au contraire 100 % vierge, selon les attentes de nos clients. Ils sont toutefois de plus en plus rares à ne pas vouloir de PET recyclé dans leurs préformes. » Outre le milliard de préformes qui sort chaque année de l’usine de Sainte-Marie-la-Blanche, Plastipak en réalise 40 milliards par le biais de ses différents sites dans le monde, difficile d’être passé à côté.
Nadège Hubert
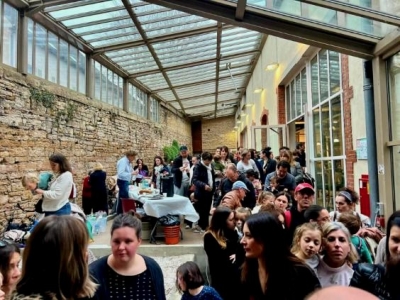
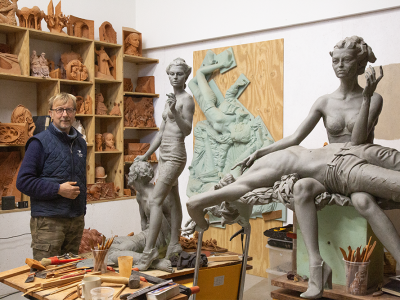
-
Beaune - Fini le brûlage ? La viticulture beaunoise explore de nouvelles voies pour les sarments
-
Salon de l’Habitat de Chevigny : plus de 30 exposants pour faire le plein de bonnes idées pour son logement
-
Météo en Côte-d’Or – Une semaine sous le signe du soleil et de la douceur
-
Accident sur l'A31 près de Beaune : circulation perturbée
-
Un investissement stratégique pour la Haute-Saône à la Base Aérienne 116
-
Le Conseil Départemental de Côte-d’Or investit massivement pour l’agriculture et le monde rural
-
Bligny-lès-Beaune – Adeline Henriot, une battante déterminée à briser les préjugés pour Miss Beauté Bourgogne 2025
-
Beaune - Succès éclatant pour les 30 ans d’Arc en Ciel : une fête intergénérationnelle et joyeuse
-
Sécurité routière et lutte contre les trafics - 600 véhicules inspectés et de nombreuses infractions relevées lors d’un contrôle massif sur l'A6
-
Cité des Climats de Beaune - L'Aligoté en Bourgogne : d'un passé modeste à un avenir radieux
-
Retour de la liaison TGV Dijon-Roissy : un engagement pour 2027
-
Beaune - Début des travaux près des Urgences du centre hospitalier : impacts sur l’accès et l’organisation du service
-
Changement d’heure ce week-end : une heure de moins… mais plus de soleil !
-
De Champforgeuil (71) à Meursanges (21) - Emmanuel Joussot – Alexis Dubois : une transmission exemplaire
-
Beaune - Une nouvelle observation publique pour l’éclipse partielle de Soleil ce matin place Carnot
-
Beaune - Un vaste plan de restauration des rues pavées en préparation
-
Le Conseil Départemental de Côte-d’Or avance sur le projet de légumerie et de maraîchage
-
Maison Chanzy à Puligny-Montrachet – Luca Flaminio aux commandes du restaurant éphémère
-
Beaune - Circulation, sécurité et grands projets : ce qu’il faut retenir de la réunion publique des quartiers de la Gare et de la route de Seurre
-
Saint-Vincent Tournante 2026 - La boutique en ligne est lancée pour préparer l’événement à Maranges
-
Prestige Auto Beaune 2025 - L'événement automobile de l'année du 16 au 18 mai au Palais des Congrès !
-
Abbaye de Cîteaux - Une souscription publique pour sauver le définitoire